by Jens Thiemann, Management 3.0 Facilitator from Germany. Jens supports managers and leaders in using simple, everyday methods to build trust and improve their teams and organizations. He truly believes in the power of continuous improvement. In his workshops, he not only teaches the growth mindset and practices but also the way to implement them, so that you can immediately apply what you have learned. He is now applying the same approach in this article on continuous improvement.
In this article:
- Definition of Continuous Improvement
- Benefits of Continuous Improvement
- Strategies to Establish Continuous Improvement
Today, many companies see value in “becoming agile.” They want to remove bureaucracy and make better business decisions faster.
One pitfall is that they believe that becoming agile is a stable status, a fixed goal. They often “implement” a specific approach and introduce it like a traditional project, with meticulous planning and a timed roadmap.
But if you understand agility in a business scope, you know you need to prepare and react to the unknown. You can never stand still, but you must continuously adapt and improve. Instead of optimizing for the following fixed state, companies should organize to adapt and improve continuously.
I just learned from a friend who works for a larger corporation that they implemented the Spotify model. They invited a more prominent consulting firm, which helped them with their implementation roadmap. One step in their checklist was that they needed 35 product owners, so they organized a two-day training and helped the employees pass the required test. Ta-da, just 48 hours later, they reached this milestone. No need to explain that none of these people had become agile or were ready to “deliver” continuous improvements.
Unfortunately, or luckily, each company is different, and it will not work to imitate what another company is doing. This is why too many digital transformations have failed and why each company needs to find their own way of working.
So, what do you need to do differently, and why is it business-critical to aim for continuous improvements?
What Is Continuous Improvement?
Continuous improvement is consistently refining and enhancing processes, products, and services. Originating from the Japanese philosophy of Kaizen, which means “change for the better,” continuous improvement is nowadays used in many companies and became part of the agile methodologies.
Kaizen is a Japanese philosophy that means “continuous improvement,” focusing on making small, incremental changes to enhance productivity, efficiency, and quality. It involves everyone in an organization, from top management to frontline workers, encouraging them to contribute ideas for improvement. The approach emphasizes standardizing successful changes, reducing waste, improving processes, and solving problems systematically. Kaizen fosters a culture of teamwork and ongoing progress, ensuring that improvements are sustainable and build upon each other over time.
The Plan-Do-Check-Act-Cycle from Edwards Deming which is part of the Management 3.0 Change Model is a well-known and easy-to-understand technique. This feedback loop inspires people and teams to inspect their work regularly. Agile product development manifests the PDCA cycle in incremental deliveries, often due to a sprint followed by a retrospective.
While it is often implemented within a team, the real challenge is to move this way of working to the organizational level, making it a company-wide operational model.
For an organization, continuous improvement is more than just a bunch of teams delivering products regularly. It requires improving its way of working, which impacts team setups, decision-making, role assignments, and more. Given the future’s unpredictability, the ability to deliver and adapt quickly is crucial. This skill ensures they remain efficient and competitive.
Benefits of Continuous Improvement for Teams, Products, and Organizations
Why should you invest time and strive for continuous improvement?
Continuous Improvement Fosters Enhanced Team Collaboration
With a continuous improvement approach, teams regularly engage in retrospectives to discuss what went well and what requires improvement. Retrospectives encourage team members to voice their opinions and ideas; they learn how to give and receive feedback and how to deal with conflicts, leading to a more inclusive and motivated work environment. As a result, team morale improves, and collaboration becomes more effective.
Higher Quality Products through Continuous Improvement
By continuously refining processes and incorporating feedback, the quality of products and services improves. Regular testing and iteration ensure that defects are identified and addressed promptly, leading to more robust, reliable products that meet or exceed customer expectations. By focusing o n the right product features, teams can deliver faster , and time-to-market speeds up.
Continuous Improvement Leads to Increased Organizational Efficiency and Innovation Capability
Organizations that embrace continuous improvement can identify and eliminate inefficiencies in their processes. Their managers understand how to delegate decision-making and avoid being a bottleneck by empowering teams and setting constraints. The delegation levels and the Delegation Boards are praxis-proven and widely praised tools. Together with good goal-setting, this reduces waste and results in faster reaction times.
With avoiding wasting time in useless products, organization gains time to be invested in experimenting with new ideas and approaches. So, continuous improvement equips organizations with the ability to respond swiftly to market demands and to invest into technological advancements.
Become attractive to Talents and Employees through Continuous Improvement
One often underestimated benefit of an adaptable organization is they become attractive for talents and increase employee happiness. Why? Because the adaptability allows to ability to run short projects formed by different people. This allows people to switch their context, so they can learn and to grow personally.
Improvement sometimes means taking two steps forward and one step back. Teams must go through both gradual and radical changes, taking small steps and big jumps in order to navigate the often challenging landscape.
Jurgen Appelo, How to Improve Everything
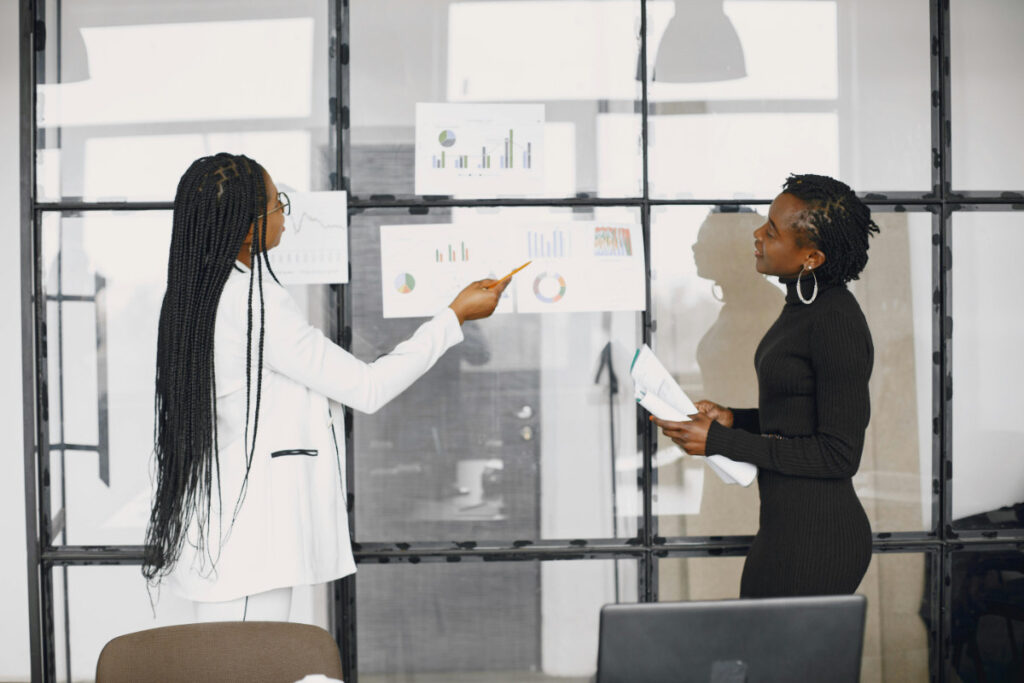
Promoting Continuous Improvement in the Workplace
Continuous improvement fosters a culture of open communication and collaboration. Or, you can argue that you need a culture of trust, open communication, and collaboration formed by people with a growth mindset. All of this matches the principles and practices of Management 3.0. Developing this culture and mindset requires time for personal development and organizational alignment, which – unluckily – organizations often ignore.
Cultivating a Continuous Improvement Culture
Creating a culture that values continuous improvement is essential. This involves encouraging open communication, promoting a growth mindset, and recognizing the efforts of team members who contribute to process enhancements. Leaders play a crucial role in setting the tone and modeling continuous improvement behaviors.
Management 3.0 emphasizes the importance of empowering teams and fostering a culture of continuous improvement. The various workshops help teams explore other ways of working and celebrate small wins, reinforcing the continuous improvement mindset.
As said in the beginning, companies are different, and there is no one-size-fits-all approach. If you want to start changing your organization and take the first steps to continuous improvement, guidance, communication, and trust are key factors. Here, the Change Management Game questions are a valuable tool to evaluate your understanding and communication abilities.
Avoid “implementation projects” and do not assume a culture change will occur due to a major reorganization. This change will take time. Please avoid spending months preparing the change within a small leadership team and then expecting the entire organization to adapt after a single town hall meeting.
Promoting Continuous Improvement through Providing Time and Letting It Evolve
Make sure your teams and leaders have time to adapt. You must provide time for training, personal development, and alignment. Workshops, seminars, and online courses on agile methodologies, lean principles, organizational design, and Management 3.0 mindset and practices can be highly beneficial.